Shock and vibration isolators are essential components for Wire Rope Isolators protecting equipment from the damaging effects of constant movement and impact. When it comes to choosing the best shock and vibration isolators for your equipment, it's crucial to consider various factors such as the type of equipment, environmental conditions, and specific isolation requirements. By selecting the right isolators, you can ensure the longevity and optimal performance of your equipment. In this article, we will explore the key considerations for choosing the best shock and vibration isolators for your equipment to help you make an informed decision.
When choosing the best shock and vibration isolators for your equipment, it is important to consider the specific requirements and conditions of your application. Factors to consider include the weight and size of the equipment, the level of shock and vibration it will be subjected to, and any specific environmental factors such as temperature or moisture. Additionally, it is important to evaluate the different types of isolators available, such as rubber Vibration Isolation System mounts, spring isolators, or air spring isolators. Each type has its own advantages and disadvantages, and the best choice will depend on the specific needs of your equipment. It is also essential to consider the installation and maintenance requirements of the isolators, as well as any potential compatibility issues with the equipment. Consulting with a professional engineer or vibration specialist can help ensure that the chosen isolators will effectively protect your equipment from shock and vibration.
When selecting shock and vibration isolators for equipment, it's crucial to thoroughly assess the specific needs of the application. This includes careful consideration of factors such as the size and weight of the equipment, the intensity of shock and vibration it will vibration isolators encounter, and any unique environmental conditions that may impact performance. It's also important to evaluate the different types of isolators available, such as rubber mounts, spring isolators, or air spring isolators. Each type has distinct advantages and disadvantages, making it necessary to choose one that aligns best with the demands of the equipment and its operating environment. Furthermore, examining the installation and maintenance requirements of the isolators, as well as any potential compatibility issues with the equipment, is crucial. Seeking guidance from a professional engineer or vibration specialist can help ensure the selected isolators effectively safeguard the equipment from shock and vibration.
Understanding Shock and Vibration Isolators: A Comprehensive Guide
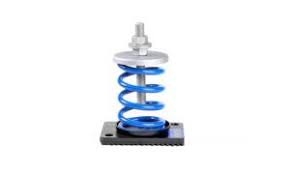
Understanding Shock and Vibration Isolators: A Comprehensive Guide is a comprehensive resource that delves into the principles, design, and applications of shock and vibration isolators. The guide covers the fundamental concepts of shock and vibration isolation, including the theory behind isolator performance and the factors that affect their effectiveness. It also discusses various types of isolators, such as rubber mounts, spring isolators, and damped systems, and provides insights into their selection and use in different industrial and engineering settings. Additionally, the guide offers practical advice on troubleshooting and maintenance to ensure optimal performance of shock and vibration isolators. This resource is an invaluable reference for engineers, designers, and anyone involved in the selection and application of shock and vibration isolators.
Types of Shock and Vibration Isolators for Industrial Applications
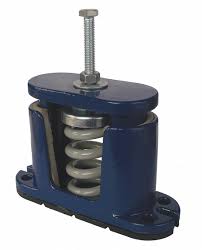
Types of Shock and Vibration Isolators for Industrial Applications include: 1. Springs: These isolators use metal springs to absorb and dampen shock and vibration. They are commonly used in machinery and equipment to reduce the impact of external forces. 2. Rubber Mounts: Rubber isolators are designed to provide a high degree of isolation by utilizing the natural resilience and damping properties of rubber. They are often used in industrial applications to mitigate the effects of vibration and noise. 3. Pneumatic Mounts: Pneumatic isolators use compressed air to cushion and isolate equipment from shock and vibration. They are suitable for sensitive instruments and high-precision machinery. 4. Elastomeric Isolators: These isolators are made of elastomeric materials such as rubber or neoprene and are effective in reducing high-frequency vibrations. They are commonly used in industrial equipment and machinery to protect sensitive components. 5. Shock Absorbers: Shock absorbers are designed to absorb and dissipate the energy generated by sudden impacts or vibrations. They are commonly used in automotive and industrial applications to protect equipment and improve safety. When selecting the appropriate type of shock and vibration isolator for industrial applications, factors such as load capacity, frequency of vibrations, and environmental conditions should be considered to ensure effective isolation and protection of equipment.
The Importance of Shock and Vibration Isolators in Machinery
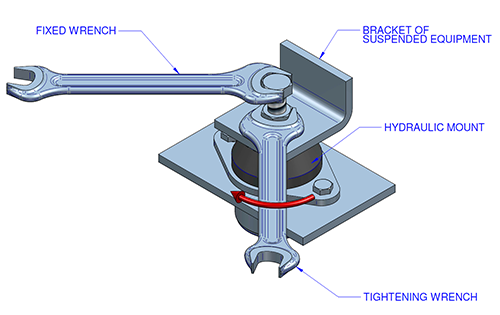
The importance of shock and vibration isolators in machinery lies in their ability to protect equipment and structures from damage caused by external forces. These isolators work by absorbing and dissipating the kinetic energy generated by shocks and vibrations, limiting their transmission to the surrounding environment. By reducing the impact of these forces, shock and vibration isolators help to extend the lifespan of machinery, improve operational efficiency, and minimize the need for frequent maintenance and repairs. Additionally, these isolators also contribute to a safer working environment by reducing the risk of equipment failure and structural damage. Overall, the use of shock and vibration isolators is crucial for ensuring the reliability and performance of machinery in various industrial and commercial applications.
Choosing the Right Shock and Vibration Isolators for Your Equipment
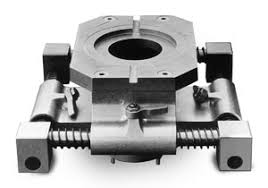
Choosing the right shock and vibration isolators for your equipment is essential to ensure the proper functioning and longevity of your machinery. There are several factors to consider when selecting isolators, including the weight and size of the equipment, the level of vibration and shock it will be subjected to, and the environmental conditions in which it will be operating. It is also important to consider the type of isolation system that will best suit your needs, whether it be passive, active, or semi-active. Taking into account all of these factors will help you choose the right isolators to protect your equipment and optimize its performance.
How Shock and Vibration Isolators Improve Equipment Performance
small vibration isolation mounts
Shock and vibration isolators are crucial in improving equipment performance as they effectively reduce the impact of external forces on sensitive machinery. By absorbing and isolating shocks and vibrations, these devices help to minimize wear and tear on equipment, extend the lifespan of components, and maintain optimal operating conditions. This ultimately results in improved reliability, accuracy, and overall performance of the equipment, making shock and vibration isolators essential for a wide range of industrial and commercial applications.
Common Problems with Shock and Vibration Isolators and How to Fix Them
Some common problems with shock and vibration isolators include: 1. Misalignment: If the isolators are not properly aligned, they may not effectively isolate shock and vibration. This can be fixed by ensuring that the isolators are correctly positioned and secured. 2. Overloading: If the isolators are carrying a load that exceeds their capacity, they may become less effective at isolating shock and vibration. This can be fixed by either reducing the load or using isolators with a higher capacity. 3. Wear and Tear: Over time, shock and vibration isolators can experience wear and tear, reducing their effectiveness. This can be fixed by regularly inspecting and replacing isolators as needed. 4. Improper Installation: If the isolators are not installed correctly, they may not function as intended. This can be fixed by following the manufacturer's guidelines for installation. To prevent and address these issues, it's important to regularly inspect and maintain shock and vibration isolators, and to ensure that they are being used within their specified capacity and parameters. If issues persist, it may be necessary to consult with a professional for further assistance.
The Future of Shock and Vibration Isolators: Innovations and Developments
The Future of Shock and Vibration Isolators: Innovations and Developments examines how advancements in materials, technology, and design are shaping the future of shock and vibration isolation systems. The book covers topics such as new materials for isolators, innovative designs for more effective vibration control, and emerging technologies that are driving improvements in shock and vibration isolation. It also explores how these advancements are impacting industries such as automotive, aerospace, defense, and manufacturing. Additionally, the book discusses the potential future trends and developments in the field of shock and vibration isolators.
Benefits of Using Shock and Vibration Isolators in Various Industries
1. Increased equipment lifespan: Shock and vibration isolators help protect machinery and equipment from the damaging effects of constant vibration and shock, thereby extending their useful lifespan. 2. Improved product quality: By reducing the impact of shock and vibration on manufacturing equipment, isolators contribute to the production of higher quality goods and minimize the likelihood of product defects. 3. Enhanced worker safety: Isolators can help mitigate the transmission of harmful vibrations to workers, promoting a safer and more comfortable work environment. 4. Reduced maintenance costs: Minimizing the impact of shock and vibration can lead to decreased maintenance and repair expenses by preventing premature wear and damage to equipment components. 5. Compliance with industry regulations: Many industries have strict guidelines regarding acceptable levels of vibration, and utilizing isolators can help companies meet these requirements and ensure regulatory compliance. 6. Greater precision and accuracy: Shock and vibration isolators can help maintain the stability and accuracy of sensitive equipment such as measuring devices, optical instruments, and precision machinery. 7. Energy efficiency: By reducing the amount of energy wasted on unnecessary vibrations, isolators can help improve the overall energy efficiency of industrial operations. 8. Environmental protection: Minimizing vibration and shock can help reduce noise pollution and limit the environmental impact of industrial equipment on surrounding areas.
In conclusion, when it comes to choosing the best shock and vibration isolators for your equipment, it is important to consider the specific requirements and conditions of your application. By carefully evaluating factors such as load capacity, frequency of vibration, and environmental factors, you can ensure that your equipment is effectively protected from damaging shocks and vibrations. Shock and vibration isolators play a crucial role in maintaining the performance and longevity of your equipment, making it essential to select the right isolator for your needs.
See also
https://www.vibrationmounts.com/vib/catalog/vibration-isolation-products.aspx https://www.hkm.com/vibration-isolation